Audi e-tron electric motors & setup
Audi e-tron has powerful electric motors and was the first EV to have a tri-motor configuration. Audi e-tron has 3 different motor configurations.
Motor configuration
They have designed two induction motors (asynchronous motors) that are used in the 3 different configurations.
Audi e-tron 50 quattro, e-tron 55 quattro and e-tron S uses the same motors but in different configuration.
It is one with 247Nm torque called 250 and one with 314Nm torque called 320. They are used in different configurations on the different models.
On e-tron 50 on e-tron 55 they have the 250 in front with a parallel (APA250) axle and the 320 rear with coaxial axle (ATA320). In e-tron S they have the 320 in front (APA320) and two 250 in the back (ATA250)
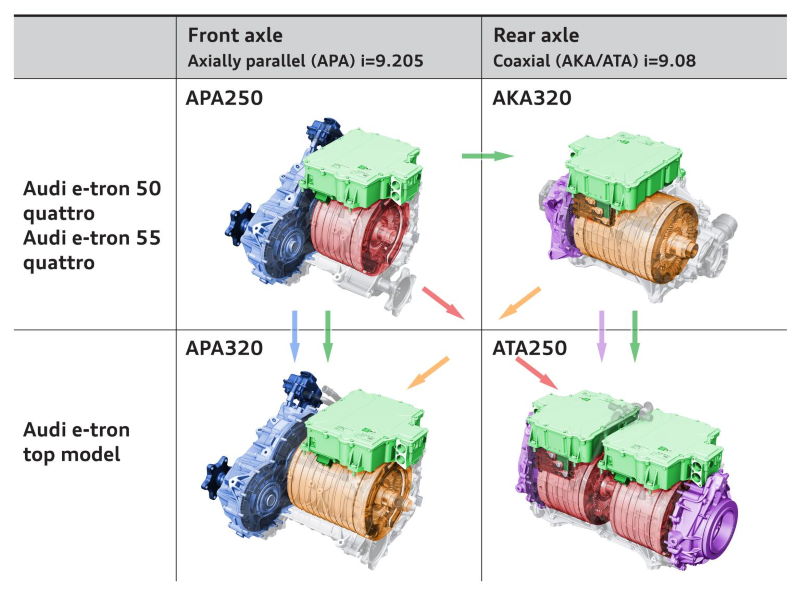
Motor configuration
The table below summarizes the performance for the version
APA250 | ATA320 | APA320 | 2 x ATA250 | |
---|---|---|---|---|
Power | 125 kW | 140kW | 129kW | 205 kW |
Power w/boost | 135 kW | 165 kW | 157 kW | 276 kW |
Torque | 247 Nm | 314 Nm | 314 Nm | 494 Nm |
Torque w/booost | 309 Nm | 355 Nm | 355 Nm | 618 Nm |
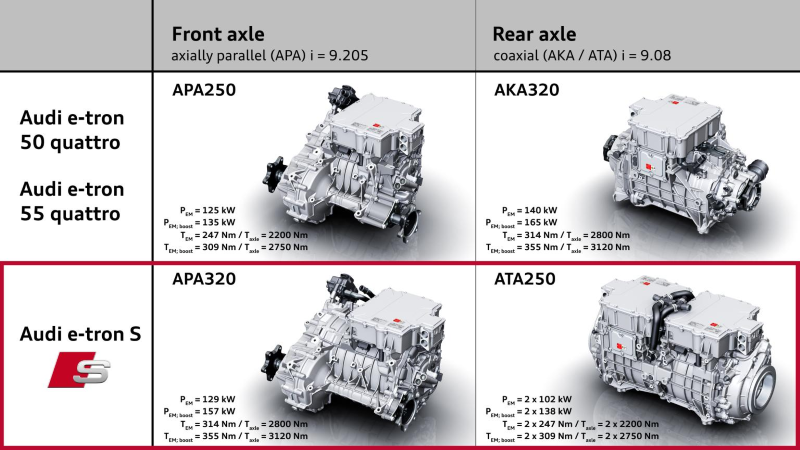
Electric motor performance figures
Drivetrain motor setup
Audi e-tron 55 & Audi e-tron 50 motor setup
For both e-tron 50 and e-tron 55 Audi uses the AKA320 drive unit for the rear. This is a drive unit with 314nm torque (355nm with boost on e-tron 55) and it has a coaxial configuration on the axels (axels goes through the unit)
The motors have a 2 stage plantaery gear differentsial
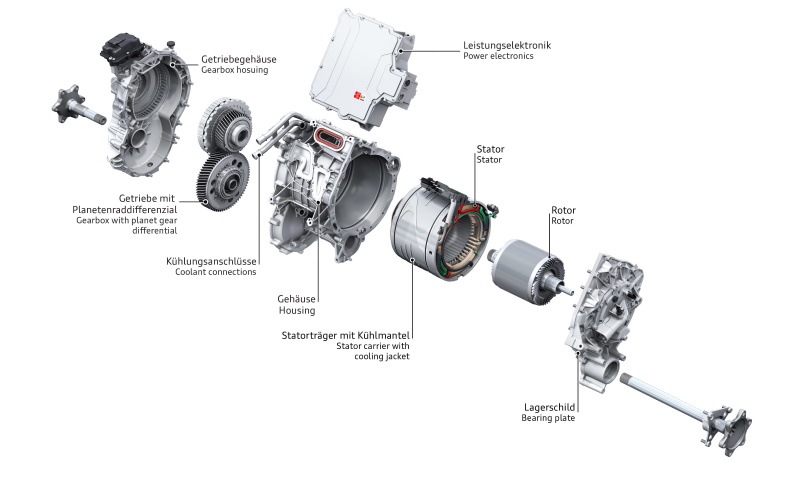
Front electric motor with power electronics
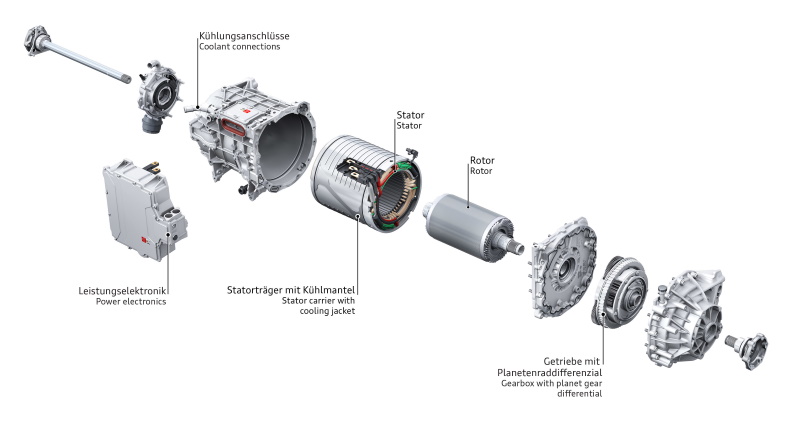
Rear electric motor with power electronics
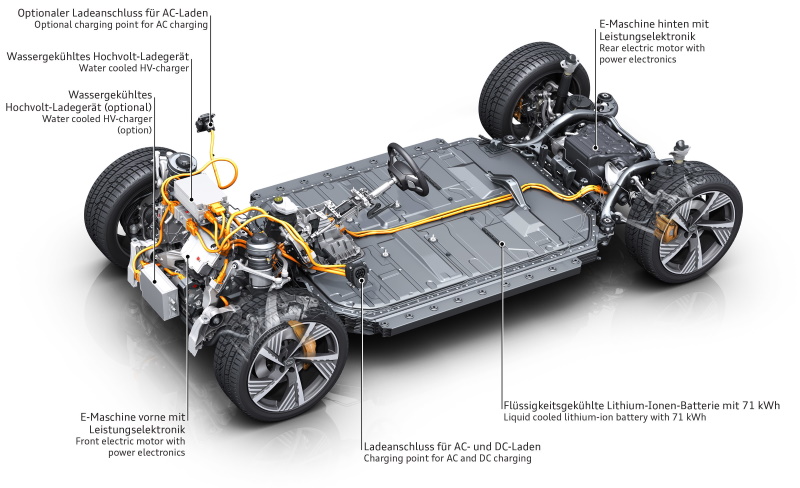
e-tron 50/55 drivetrain with electric motors
Audi e-tron 60S
In the e-tron S model Audi has moved the rear motor from e-tron 50 and e-tron 55 to the front and taken two front motors and combined them together on the rear axle.
2 x 138 kW boost power / 2 x 70kW continuous power / 2 stages, 1 gear / liquid cooled
Total 155kg.
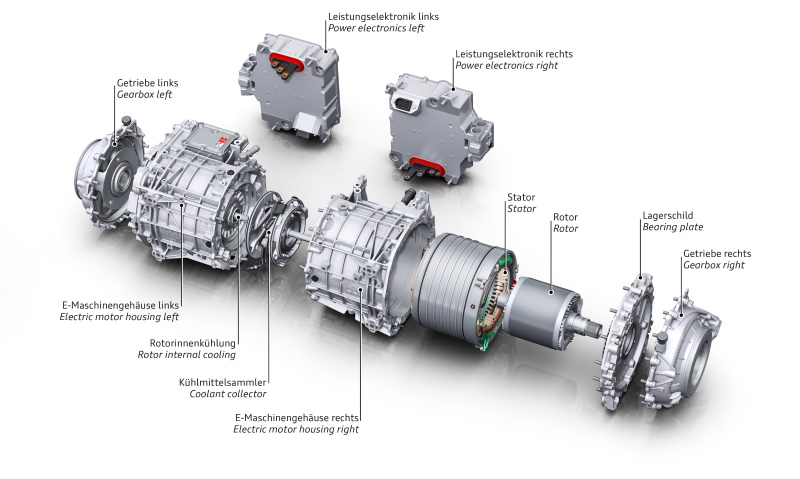
Rear electric motor with power electronics
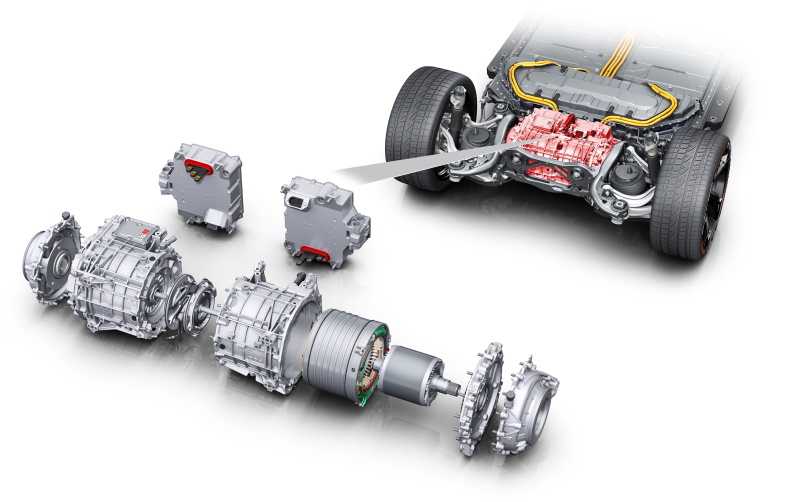
Rear electric motor with power electronics
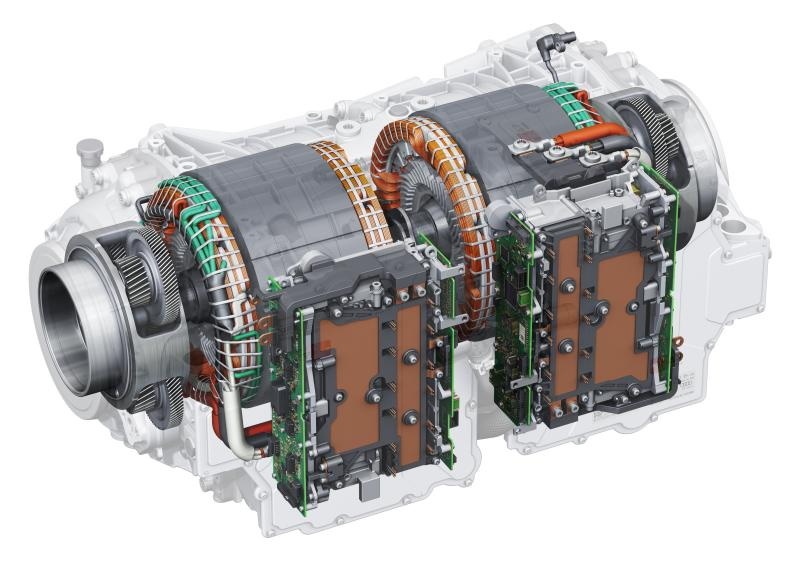
Rear electric motor with power electronics
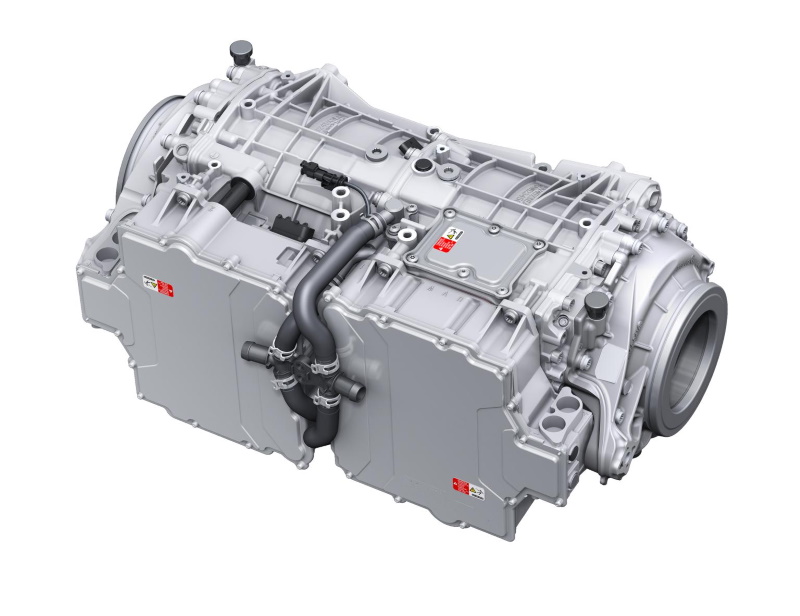
Rear electric motor with power electronics
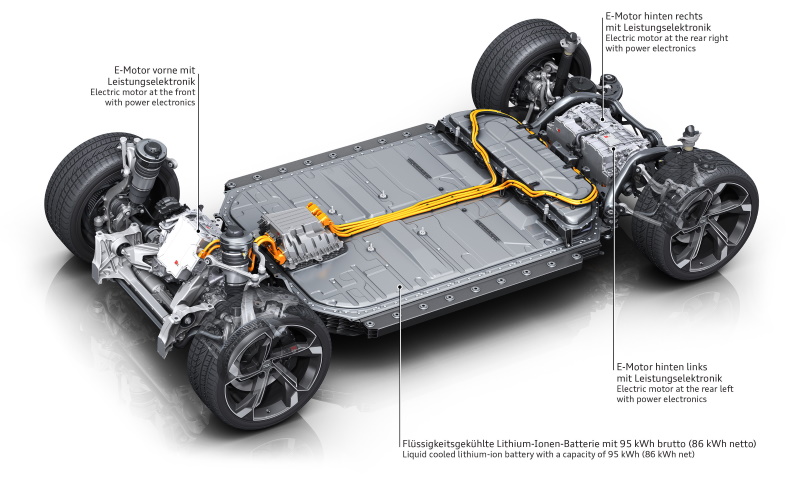
e-tron s drivetrain with electric motors
This technical animation shows the total axle drive set up in the Audi e-tron S.
Animation of the drivetrain construction, twin motor, and coolant circuit of the Audi e-tron S Sportback.
Cooling
Each motor has liquid stator cooling, bearing plate cooling, and rotor internal cooling that Audi e-tron maximum thermal robustness under all operating conditions.
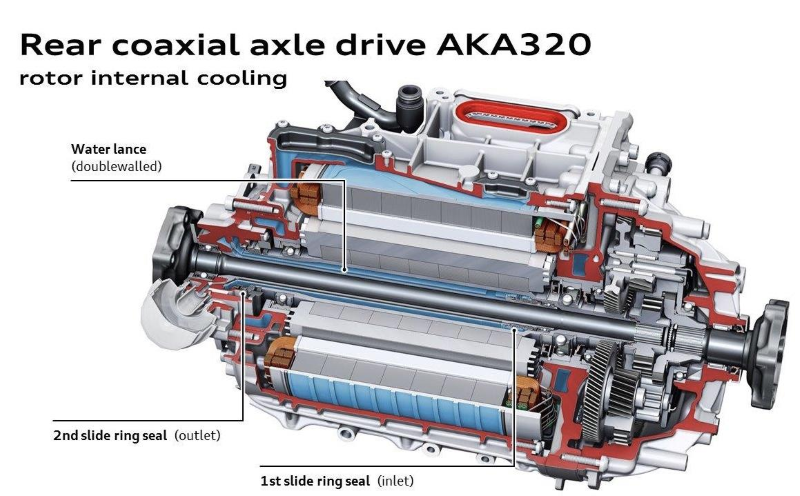
Cooling
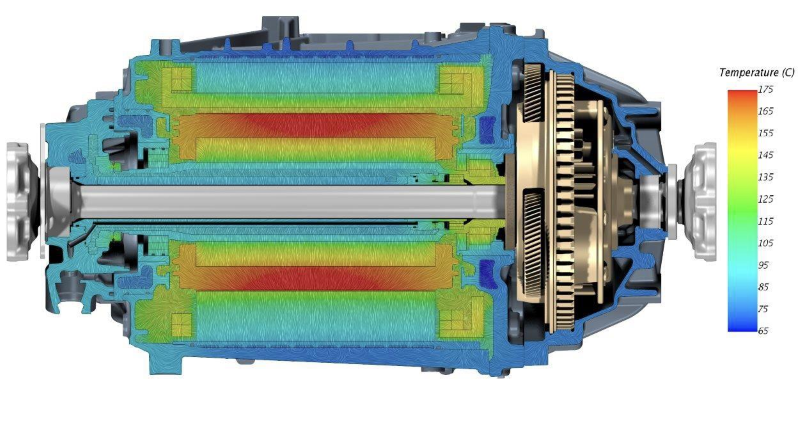
Cooling
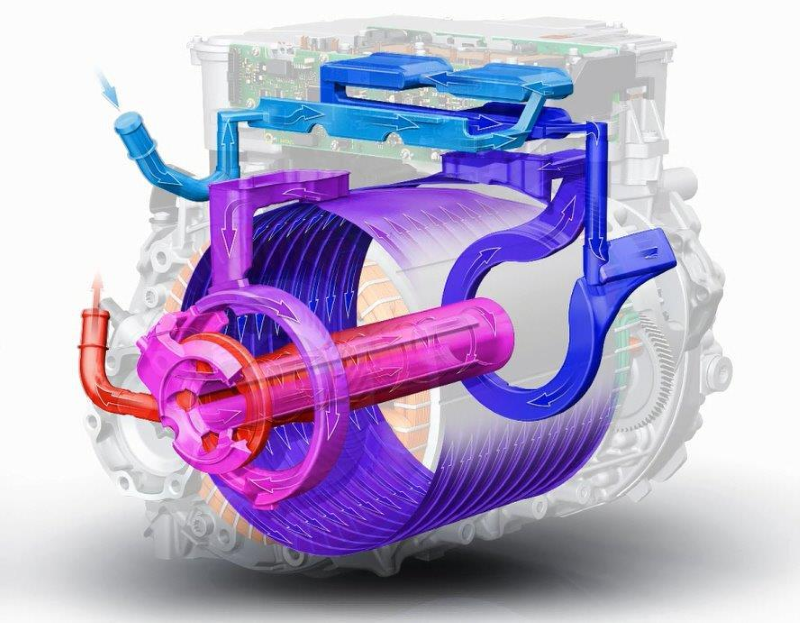
Cooling
This diagram shows how the rotor internal cooling helps keep the temperature low.
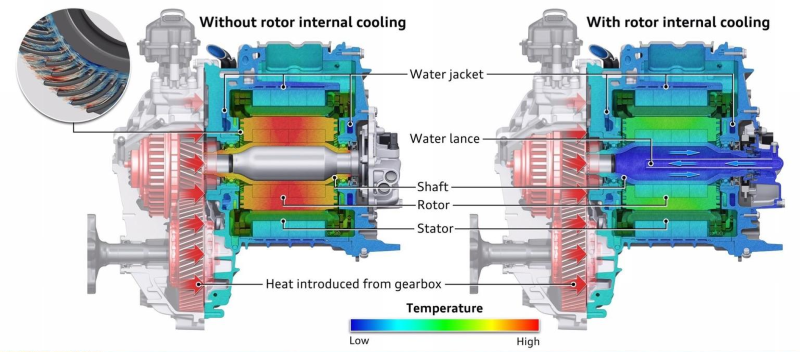
Cooling
This animation shows the cooling and heat dissipation of the twin-coax drive.
Brake recuperation: output of up to 265 kW
While braking, the electric motors perform decelerations alone up to around 0.3 g, i.e. the vast majority of all brake applications in everyday driving. The hydraulic wheel brakes are activated only when the driver brakes very heavily. The transition is almost unnoticeable, and recuperation remains active almost up to a standstill. If both electric motors are involved in brake recuperation in order to ensure handling stability, they can recover up to 275 kW of power. In all driving situations – be it full acceleration, dynamic handling, coasting or brake recuperation – the Audi e-tron remains unshakably stable because its control systems for brakes, suspension, drive, and power electronics are closely connected and work together quickly.
Differential and electric torque vectoring
In addition to electric all-wheel drive, Audi e-tron S are equipped with electric torque vectoring:
For reasons relating to efficiency, the rear electric motors in the Audi e-tron S and e-tron S Sportback provide propulsion when driving normally. The front electric motor is deenergized, but flashes into action when the driver demands more output, or predictively before slip occurs when driving on slippery roads or cornering at high speed. This electric all-wheel drive is now being enhanced with electric torque vectoring at the rear axle: Each of the two electric motors send their torques directly to the wheel via a transmission; there is no longer a mechanical differential.
Thanks to the spontaneity of the electric motors, electric torque vectoring, that is the distribution of the torque between the rear wheels, takes place within milliseconds. The time offset as compared to a mechanical system is shorter by a factor of four. It can also manage considerably higher torque: When the driver accelerates out of a corner at a sporty speed, the outside rear wheel is subject to 220 Nm (162.3 lb-ft) more than the inside wheel. Due to the gear ratio, the difference at the wheels is around 2,100 Nm (1,548.9 lb-ft). The yaw moment that is generated supports the steering characteristics and the curve radius can be retained with a smaller steering angle. Electric torque vectoring also offers great strengths in terms of pure traction: If one of the rear wheels is on very slippery ground during acceleration, e.g. a patch of ice or gravel, it receives no torque. Almost all of the torque is transferred to the wheel that has stronger traction.
A prerequisite for the high speed and precision with which the electric all-wheel drive and the electric torque vectoring work is the close linking of the following control units: the Electronic Stabilization Control (ESC), the drive control unit (ASG), the electronic chassis platform (ECP), and the control units of the performance electronics, which output voltage pulses up to 10,000 times per second. All software functions, apart from the ESC, are Audi in-house developments that benefit from the brand’s roughly 40 years of quattro experience.
The ECP is the mastermind among the control units: It makes the crucial contribution to the management of the all-wheel drive and electric torque vectoring. It calculates the ideal distribution of longitudinal and transverse torque on the basis of the data from the sensors that continuously inform it on the car’s driving condition and the driver’s request. One of its tasks is wheel-selective torque control: At the dynamic limit, the unloaded front wheel on the inside of the curve is braked slightly via the wheel brake. This minor, almost unnoticeable intervention prevents slip and makes handling even more agile and neutral.
Audi all-electric models
Click on link for direct access to the different model info for Audi all-electric models